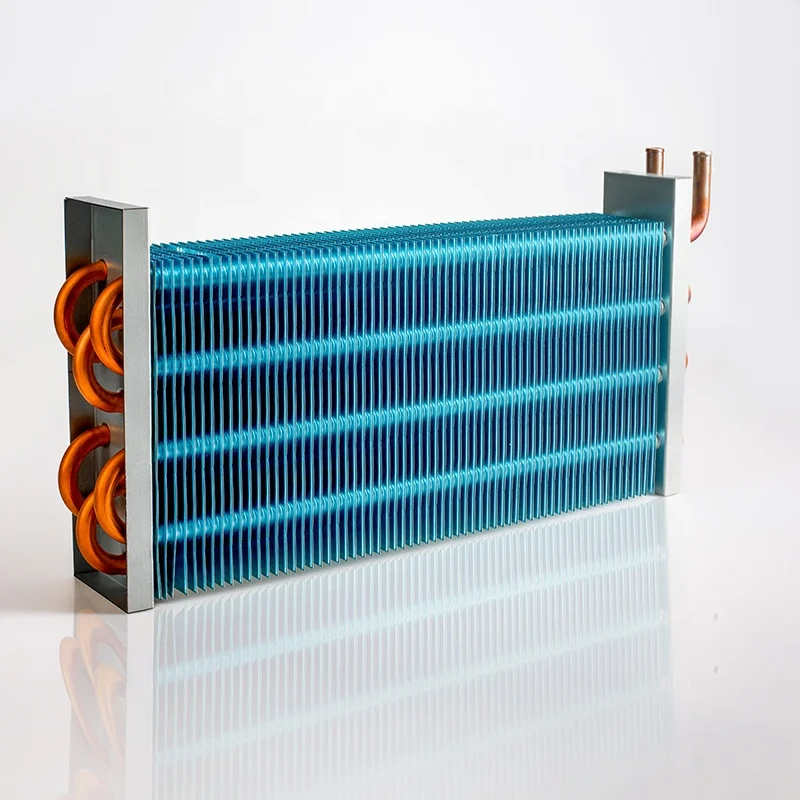
© 2025 Condenser Coil All rights reserved.
This article explains how water chillers work, focusing on the role of water in the cooling process. You will learn whether chiller water flows through the condenser coil and understand the differences between air-cooled and water-cooled systems. This is essential reading for anyone involved in HVAC, facilities management, or simply curious about how large-scale cooling systems function.
A chiller is a machine that removes heat from a liquid via a vapor-compression or absorption refrigeration cycle. This liquid can then be circulated through a heat exchanger to cool air or equipment as required. In the context of HVAC systems, chillers are used to cool water, which is then used to cool and dehumidify air in commercial buildings, industrial facilities, and other large spaces. Cold Shot Chillers is a company that can provide all needed technical support and advice when it comes to chillers.
Chillers work on the principle of refrigeration, which involves the phase change of a refrigerant from a liquid to a gas and back to a liquid. This process absorbs heat from the water, lowering its temperature. The chilled water is then used to cool the air or equipment. The basic components of a chiller system include a compressor, condenser, evaporator, and an expansion valve. The compressor raises the pressure and temperature of the refrigerant gas. The condenser then cools the high-pressure gas, causing it to condense into a liquid. The liquid refrigerant then passes through an expansion valve, which reduces its pressure and causes it to evaporate. The evaporator is where the chilled water is produced.
A chiller system cools water by transferring heat from the water to the refrigerant in the evaporator. The water enters the evaporator, which contains a series of tubes or a shell and tube heat exchanger. The refrigerant flows through these tubes at a low temperature and pressure, absorbing heat from the water. As the water absorbs heat from the refrigerant, it boils and turns into a vapor.
The chilled water, typically at around 40-45°F (4-7°C), is then pumped out of the evaporator and circulated throughout the building or process to provide cooling. The refrigerant vapor is then drawn into the compressor, where the cycle begins again. The efficiency of this heat transfer process is critical to the overall performance of the chiller. Proper water flow and temperature control are essential to ensure the chiller operates at its maximum capacity. Water chillers use heat transfer to absorb heat from the room and transfer it outside, where it is released into the air. The result of this heat exchange is that the water in the cooling tower is cooled.
The condenser is a crucial component of a chiller. Its primary function is to remove heat from the high-pressure refrigerant gas, causing it to condense back into a liquid. The condenser receives the hot, high-pressure refrigerant vapor from the compressor. Inside the condenser, the refrigerant flows through a series of tubes or coils. The condenser then uses either water or ambient air to cool and condense the refrigerant.
In a water-cooled condenser, water is circulated through the tubes surrounding the refrigerant lines. The heat from the refrigerant is transferred to the water, causing the refrigerant to condense. The warmed condenser water is then typically sent to a cooling tower for further cooling. In an air-cooled condenser, ambient air is blown across the condenser coils to cool the refrigerant. The condenser works to remove the heat absorbed by the refrigerant in the evaporator, preparing it for the next stage in the refrigeration cycle. The condenser water absorbs heat, lowering the temperature of the refrigerant.
No, the chilled water produced by the chiller does not circulate through the condenser coil. The chilled water and the condenser water are part of two separate loops within the chiller system. The “chilled water” loop is responsible for delivering cooling to the building or process. The condenser water loop is responsible for removing heat from the refrigerant in the condenser. The chiller may be connected to the cooling tower via the condenser water loop.
The chilled water flows through the evaporator, where it is cooled by the refrigerant. It is then pumped to air handling units or other cooling equipment throughout the building. The condenser water, on the other hand, flows through the condenser, where it absorbs heat from the refrigerant. It is then typically sent to a cooling tower to be cooled before returning to the condenser. The two loops are kept separate to prevent contamination and ensure efficient operation of the chiller.
A water-cooled condenser uses water to cool and condense the hot, high-pressure refrigerant gas from the compressor. The condenser is typically a shell and tube heat exchanger, where the refrigerant flows through the tubes and water flows through the shell surrounding the tubes. The cool water absorbs heat from the refrigerant, causing the refrigerant to change phase from a vapor to a liquid, and then the refrigerant returns to the evaporator to repeat the cooling cycle.
The water enters the condenser at a lower temperature, typically from a cooling tower or other water source. As the water passes through the condenser, it absorbs heat from the refrigerant, increasing its temperature. The warm water then leaves the condenser and is sent back to the cooling tower to be cooled again. This continuous circulation of water allows the condenser to effectively remove heat from the refrigerant and maintain the efficiency of the chiller system. Water-cooled condensers are commonly used in large commercial and industrial chillers due to their high efficiency and ability to handle large cooling loads.
A cooling tower is a heat rejection device that is used to cool the warm water coming from the condenser of a water-cooled chiller. The cooling tower works on the principle of evaporative cooling. Warm water from the condenser is sprayed over a fill material, which provides a large surface area for water-to-air contact. As ambient air is drawn through the tower by a fan, a small portion of the water evaporates.
This evaporation process absorbs a significant amount of heat from the remaining water, effectively lowering its temperature. The cooled water then collects in a basin at the bottom of the tower and is pumped back to the chiller’s condenser to continue the cooling process. Cooling towers are essential components of many water-cooled chiller systems, especially in large buildings and industrial applications. They provide an efficient way to reject heat to the environment and maintain the optimal operating temperature of the chiller.
Cooling Tower Efficiency
Factor | Impact on Efficiency |
---|---|
Ambient Temperature | Lower ambient temperatures generally result in better cooling tower performance. |
Humidity | Lower humidity allows for more efficient evaporation and better cooling. |
Water Flow Rate | Proper water flow rate is crucial for optimal heat transfer and cooling. |
Air Flow Rate | Adequate air flow ensures sufficient contact between water and air for effective evaporation. |
Water Quality | Clean water, free of contaminants and scale, helps maintain heat transfer efficiency. |
Maintenance | Regular cleaning and maintenance of the fill material, nozzles, and other components are essential for optimal performance. |
An air-cooled chiller is a type of chiller that uses ambient air instead of water to cool the refrigerant in the condenser. Unlike water-cooled chillers that require a cooling tower and a separate water loop, air-cooled chillers are a self-contained system. They use fans to force air over the condenser coils, which contain the hot, high-pressure refrigerant. The refrigerant condenses as the heat is transferred from the refrigerant to the air.
The main difference between air cooled and water cooled chillers lies in the method of heat rejection. Air-cooled chillers reject heat directly to the ambient air, while water-cooled chillers transfer heat to a water loop that is then cooled by a cooling tower or other water source. Air-cooled chillers are typically simpler to install and maintain as they do not require a separate water loop, water pump, or cooling tower. However, they may be less efficient than water-cooled chillers, especially in hot climates, as their performance is directly affected by the ambient temperature. The choice between a split system with an air cooled chiller or a water cooled one depends on several things, including the availability of water and the desired efficiency.
Proper water treatment and regular maintenance are crucial for the efficient and reliable operation of water-cooled chillers. Water treatment is essential to prevent scaling, corrosion, and biological growth within the chiller system. Scaling occurs when minerals in the water deposit on the heat transfer surfaces, reducing the chiller’s efficiency. Corrosion can damage the chiller’s components, leading to leaks and reduced performance. Biological growth, such as algae and bacteria, can foul the water and create health hazards.
Regular maintenance, including cleaning the condenser and evaporator tubes, checking refrigerant levels, and inspecting the water pump and other components, is also essential. A well-maintained chiller will operate more efficiently, have a longer lifespan, and require fewer repairs. Neglecting water treatment and maintenance can result in chiller performance degradation, increased energy consumption, and costly breakdowns. Therefore, it is essential to have a comprehensive water treatment and maintenance program in place to ensure the optimal operation of the chiller system.
Water is circulated through air handling units (AHUs) as part of the cooling process in buildings that use chillers. AHUs are responsible for conditioning and circulating air throughout a building. In a system with a chiller, cold water from the chiller is pumped to the AHUs. Inside the AHU, the cold water flows through a cooling coil, which is a series of tubes with fins to increase the surface area.
As warm air from the building is drawn through the AHU, it passes over the cooling coil. The cold water in the coil absorbs heat from the air, cooling it down. The cooled and dehumidified air is then distributed throughout the building via ductwork. The water in the coil, having absorbed heat from the air, becomes warmer and returns to the chiller to be cooled again. This closed-loop system allows for efficient and effective cooling of large spaces. An air handler is often used to distribute cool air.
The choice between water-cooled and air-cooled chillers depends on several factors, including the size of the cooling load, the availability of water, energy efficiency considerations, and maintenance requirements. Water-cooled chillers are generally more efficient than air-cooled chillers, especially in hot climates, because water is a more effective heat transfer medium than air. They are also typically quieter and have a smaller footprint. Water-cooled condensers use a continuous flow of water to remove heat from the refrigerant.
However, water-cooled chillers require a cooling tower or other water source, which can increase installation and maintenance costs. They also consume water, which may be a concern in areas with water scarcity. Air-cooled chillers, on the other hand, are simpler to install and maintain as they do not require a separate water loop. They are also a better choice in areas where water is scarce or expensive. However, they may be less efficient, especially in hot weather, and can be noisier than water-cooled chillers. In general, water-cooled chillers are preferred for large cooling loads and applications where energy efficiency is a priority, while air-cooled chillers are a better choice for smaller loads or situations where water availability is limited.
Chiller Selection Guide
Factor | Water-Cooled Chiller | Air-Cooled Chiller |
---|---|---|
Cooling Load | Suitable for large cooling loads (typically > 200 tons) | Suitable for small to medium cooling loads (typically < 200 tons) |
Energy Efficiency | Generally more energy-efficient, especially in hot climates | Less energy-efficient, particularly in hot climates |
Water Availability | Requires a reliable water source (e.g., cooling tower, well, municipal supply) | Does not require a water source |
Water Consumption | Consumes water due to evaporation in the cooling tower | No water consumption |
Installation | More complex installation due to cooling tower, water piping, and water treatment system | Simpler installation, no need for cooling tower or water piping |
Maintenance | Higher maintenance due to cooling tower, water treatment, and potential for scaling/corrosion | Lower maintenance, no need for water treatment, less prone to scaling/corrosion |
Noise Level | Typically quieter operation | Can be noisier due to fans used to cool the condenser |
Footprint | Smaller footprint, as the condenser is typically smaller | Larger footprint, as the condenser requires more space for air flow |
Ambient Temperature Impact | Less affected by high ambient temperatures | Performance degrades significantly as ambient temperature increases |
Cost | Higher initial cost due to cooling tower and associated equipment | Lower initial cost, but potentially higher operating cost due to lower efficiency |
Lifespan | Can have a longer lifespan with proper maintenance | May have a shorter lifespan, especially in harsh environments |
Here are the 10 most important things to remember about chillers and the role of water in the cooling process:
I hope this article has provided you with a comprehensive understanding of how water chillers work and the role of water in the cooling process. If you have any further questions or need assistance with your chiller system, please don’t hesitate to contact Cold Shot Chillers. Let us help you make the best decision for your needs.
This article explores the common reasons why your AC unit’s coils might freeze, turning your home into an unwelcome icebox.
This article delves into the common problem of refrigerant leaks in LG split AC units, specifically focusing on the debate between aluminum and copper condenser coils.
This article explores the intricate workings of your home’s HVAC system, focusing on the vital roles of evaporator and condenser coils.
Your air conditioning unit is a complex system with many parts working together to keep your home cool and comfortable.
Air-cooled condenser coils are integral constituents of air conditioning and refrigeration apparatuses.
This article provides a comprehensive overview of AC evaporator coil replacement cost, as well as condenser coil replacement cost, helping homeowners understand what to expect when facing this type of repair.
This research investigates the enhancement of airflow dynamics and thermal transfer efficacy in multi-coil condensers through strategic coil arrangement.
This numerical investigation delves into the influence of geometric parameters of immersed helical condenser coils.
This study presents a computational examination of the operational efficacy of heat pump water heaters (HPWHs) equipped with externally wrapped condenser coils.
This article delves into the critical debate of copper versus PFC (parallel flow) condenser coils in modern air conditioner units.
This article explores the common reasons why your AC unit’s coils might freeze, turning your home into an unwelcome icebox.
This document elucidates the principal factors influencing thermal exchange between the refrigerant and the airstream within a plate finned-tube heat exchanger
This article provides a comprehensive guide on how to effectively clean your refrigerator’s condenser coils.
© 2025 Condenser Coil All rights reserved.
Fill out the form below, our team can reply in 20 minutes.