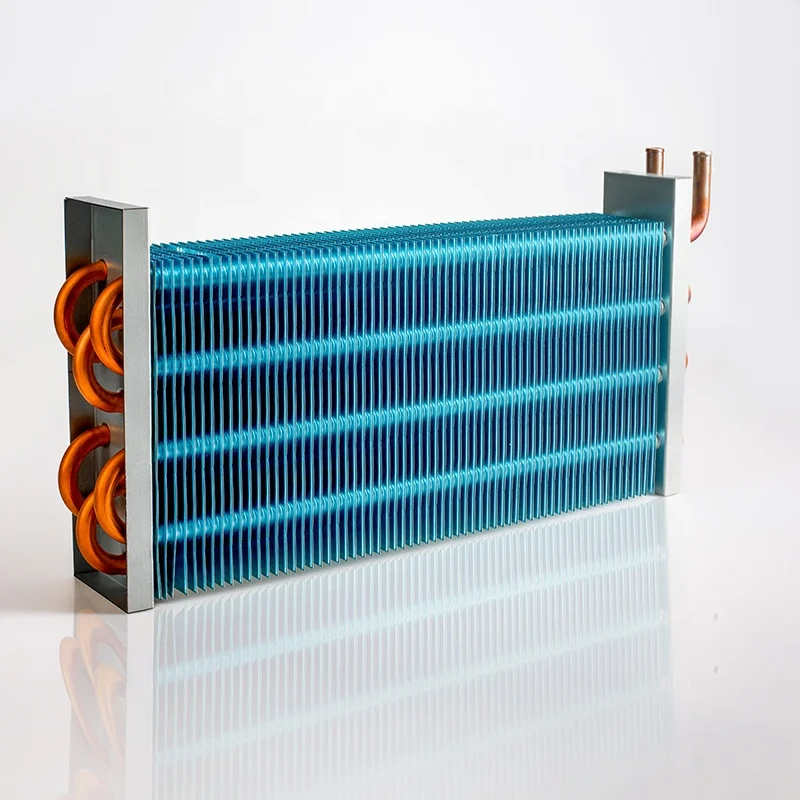
© 2025 Condenser Coil All rights reserved.
The escalating global energy demand, coupled with a growing awareness of environmental sustainability, has propelled the heating, ventilation, and air conditioning (HVAC) sector towards a paradigm shift. This study delves into the intricate domain of HVAC system optimization, focusing specifically on the condenser coil—a critical component within air-cooled direct expansion (DX) systems. By meticulously examining the interplay between thermodynamic performance and economic considerations, this research aims to provide a scientific blueprint for enhancing energy efficiency while minimizing operational costs. Traditional approaches to HVAC design often prioritize full-load conditions, overlooking the reality that most systems operate at partial loads for a significant portion of their lifecycle. This study bridges that gap by employing a sophisticated optimization methodology that considers both full and partial load scenarios. The research leverages advanced computational techniques, including transient simulation and a mixed heuristic-deterministic optimization algorithm, to analyze and optimize the condenser coil’s geometric configuration. By manipulating design variables such as fin density, tube diameter, and coil depth, this study endeavors to unlock the full potential of air-cooled DX systems, paving the way for a more sustainable and cost-effective approach to climate control.
The overwhelming majority of modern HVAC systems operate based on the vapor-compression refrigeration cycle. This cycle is a thermodynamic process that utilizes a refrigerant’s ability to absorb heat when it evaporates and release heat when it condenses. The cycle comprises four primary stages, facilitated by key components: the compressor, condenser, expansion valve, and evaporator. The compressor acts as the heart of the system, raising the pressure and temperature of the refrigerant vapor. Subsequently, the high-pressure, high-temperature refrigerant enters the condenser.
The condenser plays a pivotal role in rejecting the heat absorbed by the refrigerant from the conditioned space to the external environment. In air-cooled systems, this heat rejection is achieved by transferring heat from the refrigerant to ambient air forced across the condenser coil by a fan. The efficiency of this heat transfer process is paramount to the overall system performance. As the refrigerant releases heat, it undergoes a phase transition from a high-pressure vapor to a high-pressure liquid, a process known as condensation.
Subcooling refers to the further cooling of the liquid refrigerant below its saturation temperature at the condenser outlet. A higher degree of subcooling signifies that more heat has been removed from the refrigerant, which leads to increased refrigeration capacity and improved system efficiency. Enhancing subcooling is, therefore, a crucial aspect of optimizing the performance of the vapor-compression cycle.
The condenser coil’s heat transfer surface area is augmented by the use of fins, which are typically thin, metallic plates attached to the refrigerant tubes. The density, spacing, and geometry of these fins significantly influence the rate of heat transfer between the refrigerant and the surrounding air. A higher fin density generally translates to a larger surface area, promoting more effective heat rejection.
The diameter of the refrigerant tubes within the condenser coil affects the refrigerant flow characteristics, pressure drop, and heat transfer rate. Smaller diameter tubes offer a higher surface area-to-volume ratio, potentially enhancing heat transfer. However, they can also lead to increased pressure drop, which can negatively impact the compressor’s performance.
The depth of the condenser coil, often referred to as the number of tube rows, influences the airflow patterns and the residence time of the air within the coil. A deeper coil can provide more contact time between the air and the heat transfer surfaces, potentially improving heat rejection. However, it can also result in a higher pressure drop across the coil, requiring increased fan power.
The optimization process begins by defining an objective function, which, in this case, is the minimization of the total power consumption of the HVAC system. This function encapsulates the energy consumption of all major components, including the compressor, condenser fan, and other auxiliary equipment.
The optimization is subject to various constraints, including the physical dimensions of the condenser coil (maintaining a constant frontal area), refrigerant properties, and operating conditions. The design variables are the geometrical parameters of the condenser coil, such as fin density, tube diameter, and coil depth.
A numerical algorithm, utilizing a mixed heuristic-deterministic approach, is employed to iteratively refine the condenser coil design. This algorithm explores the design space, evaluating the performance of different configurations based on the objective function and constraints.
HVAC systems operate under constantly changing conditions, influenced by factors such as varying outdoor temperatures and fluctuating occupancy levels. Therefore, a transient simulation tool, such as TRNSYS, is essential for accurately predicting the system’s performance under these dynamic conditions.
The transient simulation model incorporates detailed mathematical representations of each system component, including the compressor, condenser, expansion valve, and evaporator. These models capture the thermodynamic behavior and interactions of the components within the system.
The simulation model is further refined by integrating experimental data collected from a real-world HVAC system. This data provides valuable insights into the actual performance characteristics of the system under various operating conditions.
A fully functioning DX rooftop package air conditioning unit serving an office building was used as the experimental setup. Sensors were installed to monitor key parameters, including refrigerant temperatures and pressures, airflow rates, and power consumption.
The integrated simulation tool was validated by comparing the predicted power consumption of the rooftop package with the actual measured data during a specific period, such as the first week of July. Close agreement between the simulated and measured data validates the accuracy of the simulation model.
Any discrepancies between the simulated and measured data were used to further refine and calibrate the simulation model, ensuring its accuracy and reliability for predicting system performance.
While enhancing energy efficiency is a primary objective, it’s crucial to consider the economic implications of design modifications. This study incorporates a thermo-economic analysis that evaluates the cost-effectiveness of different condenser coil configurations.
The analysis considers the upfront costs associated with manufacturing condenser coils with different geometries, as well as the operational savings resulting from improved energy efficiency. A trade-off approach is employed to identify the optimal design that balances these factors.
The payback period, which represents the time it takes for the energy savings to offset the initial investment, is a key metric in the thermo-economic analysis. The goal is to identify designs that offer a reasonable payback period while achieving significant energy savings.
The optimization methodology was applied to an existing DX rooftop package unit serving an office building. The building’s characteristics, including floor area, occupancy patterns, and construction materials, were meticulously modeled using the ASHRAE transfer function approach.
The operating conditions of the HVAC system, including the operating hours, indoor temperature and humidity set points, and occupancy schedule, were defined. The peak cooling load was estimated, providing a baseline for evaluating the performance of different condenser coil designs.
Parameter | Value |
---|---|
Floor Area | 325 m² |
Building Height | 3 m |
Operating Hours | 8:00 AM – 10:00 PM |
Occupant Density | 1 person/5 m² |
Peak Cooling Load | 36kW |
The validated simulation model was used to evaluate the performance of various condenser coil configurations generated by the optimization algorithm. The simulations provided insights into the energy consumption, cooling capacity, and overall system efficiency for each design.
The simulation results demonstrated a clear correlation between the condenser coil’s geometric parameters and the overall system efficiency. Variations in fin density, tube diameter, and coil depth significantly impacted the heat rejection capacity, refrigerant subcooling, and ultimately, the system’s COP.
The optimization algorithm identified several condenser coil configurations that offered substantial improvements in energy efficiency compared to the baseline design. These optimal configurations exhibited a higher COP, reduced power consumption, and enhanced cooling capacity, particularly under partial load conditions.
The optimized condenser coil designs were shown to achieve significant energy savings, potentially reducing the HVAC system’s energy consumption by a notable percentage. Moreover, the thermo-economic analysis indicated that these energy savings could be achieved with a reasonable payback period, making them economically viable.
The results of this study demonstrate the feasibility of implementing optimized condenser coil designs in real-world HVAC systems. The proposed modifications are within the realm of existing manufacturing capabilities and can be readily integrated into new or existing units.
The findings also highlight the potential for retrofitting existing HVAC systems with optimized condenser coils. This approach could offer a cost-effective way to improve the energy efficiency of older units without requiring a complete system replacement.
Future research should focus on exploring the long-term performance and reliability of optimized condenser coils under various operating conditions. Additionally, investigating the use of advanced materials and manufacturing techniques could further enhance the performance and cost-effectiveness of these designs. Also, using AI and machine learning to predict the need for maintenance could be a great direction.
Design Parameter | Baseline | Optimized Design 1 | Optimized Design 2 |
---|---|---|---|
Fin Density (fins/inch) | 14 | 18 | 20 |
Tube Diameter (inch) | 0.5 | 0.375 | 0.375 |
Coil Depth (rows) | 3 | 4 | 4 |
COP Improvement (%) | – | 8 | 10 |
Energy Savings (%) | – | 6 | 8 |
Payback Period (years) | – | 2.5 | 3 |
This study has presented a comprehensive methodology for optimizing the design of condenser coils in air-cooled DX HVAC systems. By combining advanced simulation techniques, experimental validation, and a thermo-economic analysis, this research has demonstrated the significant potential for enhancing energy efficiency and reducing operating costs. The findings underscore the importance of considering both full and partial load conditions when designing HVAC systems and highlight the critical role of condenser coil optimization in achieving a more sustainable and cost-effective approach to climate control. As the demand for energy-efficient building solutions continues to grow, the insights provided by this study will serve as a valuable resource for engineers, designers, and researchers seeking to optimize HVAC system performance and minimize environmental impact. The integration of AI-driven predictive maintenance strategies based on operational data patterns will further enhance system reliability and minimize downtime.
Your air conditioner is a crucial part of your home comfort, especially during hot weather.
This article explains how water chillers work, focusing on the role of water in the cooling process.
This step-by-step guide provides product help for homeowners looking to maintain their air conditioning system by cleaning the condenser coils.
Your air conditioner is a lifesaver during hot summer months, providing welcome relief from the heat.
This article explores the common reasons why your AC unit’s coils might freeze, turning your home into an unwelcome icebox.
This article provides a comprehensive guide on how to effectively clean your air conditioner’s condenser coil.
This article explores the critical roles of the evaporator coil vs condenser coil in your air conditioner (AC), explaining how they work together to cool your home.
This document details a study on the application of multi-objective evolutionary algorithms, specifically Genetic Algorithms (GAs).
This article explores the intricate workings of your home’s HVAC system, focusing on the vital roles of evaporator and condenser coils.
The escalating global energy demand, coupled with a growing awareness of environmental sustainability.
This article dives deep into the costs associated with copper condenser coils in split AC units.
This document details a study on the application of multi-objective evolutionary algorithms, specifically Genetic Algorithms (GAs).
This article provides a comprehensive guide on how to effectively clean your refrigerator’s condenser coils.
© 2025 Condenser Coil All rights reserved.
Fill out the form below, our team can reply in 20 minutes.