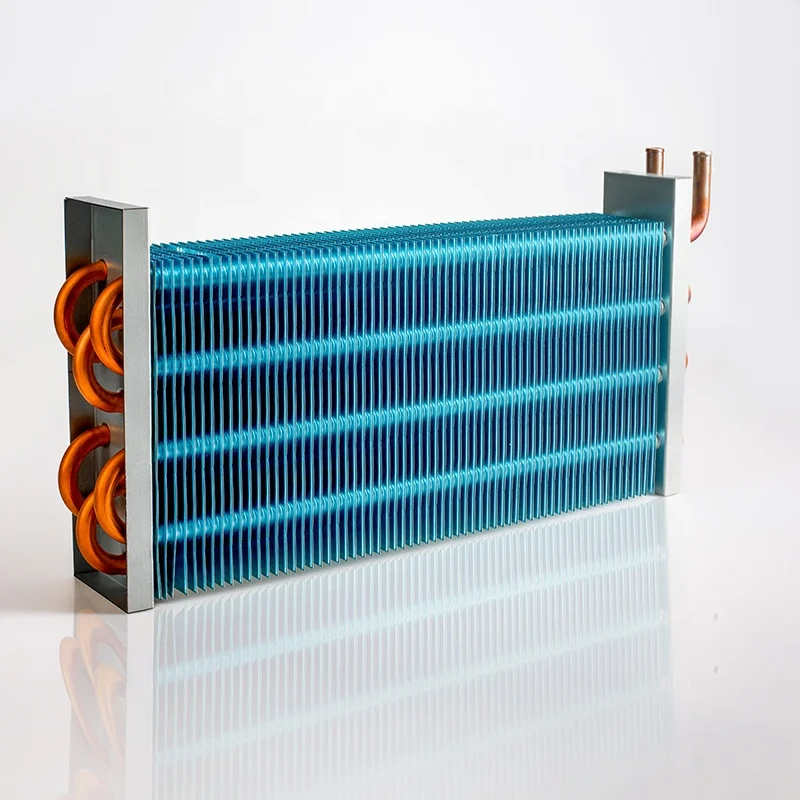
© 2025 Condenser Coil All rights reserved.
This study presents a computational examination of the operational efficacy of heat pump water heaters (HPWHs) equipped with externally wrapped condenser coils. A coupled computational model was formulated to replicate the thermal storage dynamics of a HPWH. This model integrates a multi-flux computational fluid dynamics (CFD) module, which delineates the fluid flow and thermal transport phenomena within the water reservoir, with a vapor-compression cycle simulation implemented in MATLAB to characterize the operational parameters of the system. The thermal flux across the superheated vapor, two-phase transition, and subcooled liquid zones of the condenser was derived from the system model and applied as boundary conditions for the water reservoir simulation. The computational results from the coupled model exhibited strong concordance with empirical measurements. Comparative evaluations of the heat transfer coefficient, coefficient of performance (COP), and thermal stratification within the reservoir were conducted for variable-pitch and constant-pitch condenser coil configurations. The findings indicate that the variable-pitch coil configuration yields enhancements in the heat transfer coefficient and average COP of 21.91% and 10.75%, respectively, in comparison to the constant-pitch counterpart. Furthermore, it was observed that a judicious reduction in coil pitch and diameter could elevate the mean water temperature by approximately 1°C while maintaining the maximum vertical temperature differential below 7.50°C. This investigation furnishes valuable insights for augmenting the operational efficiency of heat pump water heaters. The heat pump water heater is a useful device to decrease energy consumption.
Thermal energy demand for water heating constitutes a substantial portion of the overall energy expenditure in buildings [1], [2]. Heat pump water heaters (HPWHs) offer significant potential for energy conservation, and their deployment and utilization are actively promoted by numerous nations [3], [4]. A thorough examination and refinement of the thermal exchange dynamics between the condenser and the water reservoir are instrumental in ameliorating the thermal stratification within the storage tank [5].
Condenser configurations can be broadly classified into wrap-around and immersed coil types, contingent upon the mode of thermal interaction between the condenser coil and the water [6]. In contrast to immersed coils, wrap-around coils circumvent direct contact with water, thereby mitigating scaling and corrosion concerns. Consequently, wrap-around coils are predominantly employed in contemporary HPWH systems available in the market. The performance of heat pump water heater is constantly improved.
Current research endeavors pertaining to HPWHs primarily encompass system thermodynamics, refrigerant selection, component design optimization, and control strategies [7], [8], [9], [10], [11]. Within the domain of component design, condenser coils and water storage tanks are focal points of investigation.
In the context of HPWHs employing wrap-around coils, the optimization of the coil’s structural attributes and winding arrangement assumes paramount importance in enhancing the temperature stratification within the storage tank and augmenting overall system performance. Park and Hrnjak [12] conducted empirical investigations comparing microchannel and round-tube condensers, revealing that the COP and heat flux were superior in the microchannel condenser.
Wang [13] employed computational simulations to demonstrate that a reduction in condenser coil diameter and an increase in spiral diameter could enhance system performance. Yang, Shao, and Zhang [14] ascertained that modifying the coil’s cross-sectional configuration could marginally improve the refrigerant’s heat transfer performance within the condenser coil.
However, despite these structural modifications to the condenser coil, the thermal resistance is not substantially mitigated, and pronounced temperature stratification within the water tank persists. Consequently, further optimization of the coil winding configuration is warranted to address these limitations.
Simulation methodologies are frequently employed to scrutinize the thermal performance of water storage tanks, with a particular emphasis on the spatial temperature distribution within the tank [15], [16], [17]. The application of computational fluid dynamics (CFD) software packages for water tank modeling necessitates the imposition of appropriate boundary conditions to ensure the fidelity of the simulation results.
Conventional approaches involve the prescription of constant wall temperature or constant heat flux as boundary conditions [18], [19]. However, Jayakumar et al. [20] advocated for the adoption of more realistic boundary conditions that dynamically vary with heating time or water temperature. Lv et al. [21] acknowledged the temporal variation in condensation temperature and, accordingly, implemented a variable wall temperature boundary condition.
Dai and Li [22] formulated a polynomial function representing the temporal variation of the average heat flux of the condenser coil as the boundary condition. Nevertheless, the condenser encompasses distinct regions of superheated vapor, two-phase flow, and subcooled liquid, resulting in non-uniform heat flux distribution along the coil’s vertical extent. Therefore, a more refined approach involves partitioning the heat transfer boundary condition into three distinct regions to optimize the CFD model of the water tank, thereby enabling a more accurate representation of the actual heating process. The study of heat transfer process is essential.
The coupling of a heat pump system model with a water tank CFD model constitutes a novel simulation paradigm [22], [23], [24]. Dai and Li [22] developed an integrated model encompassing both a heat pump system model and a water tank model for residential HPWHs, simulating the thermal dynamics of the water tank during the heating process. Shah and Hrnjak [23] similarly devised a coupled model that effectively replicated the system’s operational characteristics and the transient thermal behavior within the water tank.
This study, therefore, concentrates on the development of a coupled model that incorporates a multi-heat flux CFD model of the water tank to accurately capture the heat transfer phenomena within the tank, in conjunction with a vapor-compression system model implemented in MATLAB to derive the system’s operational parameters. The thermal flux values corresponding to the superheated vapor, two-phase flow, and subcooled liquid regions of the condenser are extracted from the system model and applied as boundary conditions for the CFD simulation. The system model was used in this study.
Subsequently, the heat transfer coefficient, COP, and water temperature distribution are ascertained through simulation. The coupled model is employed to investigate the influence of various wrap-around condenser coil structural designs on the operational performance of the HPWH, with the aim of identifying the optimal coil configuration to enhance the heat transfer process between the condenser and the water, and consequently, the overall system performance.
The HPWH system under consideration primarily comprises a vapor-compression cycle and a water heating circuit, including a compressor, a water tank with an externally wrapped condenser coil, an expansion valve, and an evaporator. The condenser coil is wound around the exterior surface of the water tank, facilitating the transfer of condensation heat from the refrigerant to the water within the tank.
The structural schematic of the water tank with both constant-pitch and variable-pitch wrap-around condenser coils is depicted in Figure 1. The salient structural parameters of the system are detailed in Table 1.
Table 1: Structural Parameters of the Water Tank and Condenser Coil
Parameter | Symbol | Unit | Value |
---|---|---|---|
Tank Diameter | Dt | mm | 450 |
Tank Height | Ht | mm | 1200 |
Coil Tube Diameter | d | mm | 9.52, 12.7 |
Coil Pitch (Constant) | p | mm | 40, 50, 60 |
Coil Pitch (Variable – Top) | p1 | mm | 20-40 |
Coil Pitch (Variable – Middle) | p2 | mm | 40 |
Coil Pitch (Variable – Bottom) | p3 | mm | 40-60 |
Number of Turns (Constant) | N | – | 15 |
Number of Turns (Variable) | N | – | 11, 13 |
Coil Material | – | – | Copper |
Tank Material | – | – | Stainless Steel |
Insulation Thickness | – | mm | 50 |
During the thermal storage operation of the HPWH, the water temperature distribution within the tank and the operational parameters of the system exhibit a reciprocal influence. The system’s performance is modulated by the water temperature and the refrigerant state within the condenser. As depicted in Figure 2, the thermal exchange between the condenser coil and the water tank facilitates the transfer of heat from the condenser to the tank, thereby elevating the water temperature. The efficacy of the condenser’s heat transfer process directly impacts the heating dynamics.
The coupled model developed in this study comprises two principal components: a vapor-compression system model implemented in MATLAB and a water tank model with a wrap-around condenser coil, formulated using CFD techniques. The boundary conditions for the water tank CFD model are partitioned into three distinct regions, corresponding to the superheated vapor, two-phase flow, and subcooled liquid regimes, thereby yielding a multi-flux coupled model.
To ascertain the fidelity of the coupled model, simulations were conducted for three distinct initial water temperature conditions, and the resultant water temperature distribution parameters within the tank were extracted. The model validation process entailed a comparative analysis of the simulated average water temperature against empirical measurements documented by Dai, Li, and Ye [34]. The experimental setup employed a water tank with a volumetric capacity of 150 liters. The system model was validated.
In this comparative analysis, the length and height of the condenser coils for both the variable-pitch and constant-pitch configurations were maintained as identical, and the water tank volume was fixed at 150 liters. The specific structural parameters are delineated in Table 1.
Figure 7 illustrates the temperature distribution within the water tank for both wrap-around variable-pitch and constant-pitch coils at various time intervals during the heating process. At a heating time of 60 minutes, the average water temperatures for the variable-pitch and constant-pitch configurations were 26.90°C and 27.51°C, respectively, with a maximum vertical temperature differential at the tank’s center of 15.86°C. At t = 180 min, the average water temperature of variable-pitch coil is increased by about 1 °C compared with constant-pitch coil, and the maximum temperature difference in the vertical direction of the tank center is 7.39 °C and 8.55 °C, respectively. In addition, the temperature distribution in the tank with variable-pitch coil is more uniform.
The heat transfer coefficient and average COP for the variable-pitch coil were found to be 21.91% and 10.75% higher, respectively, compared to the constant-pitch coil. These results underscore the superior thermal performance of the variable-pitch configuration.
Table 2: Performance Comparison of Variable-Pitch and Constant-Pitch Coils
Parameter | Variable-Pitch Coil | Constant-Pitch Coil | Improvement (%) |
---|---|---|---|
Average Water Temperature (60 min) | 27.51 °C | 26.90 °C | 2.27 |
Average Water Temperature (180 min) | – | – | ~2.3 |
Maximum Temperature Difference (60 min) | 15.86 °C | – | – |
Maximum Temperature Difference (180 min) | 7.39 °C | 8.55 °C | 13.57 |
Heat Transfer Coefficient | – | – | 21.91 |
Average COP | – | – | 10.75 |
The investigation revealed that an appropriate reduction in the coil pitch can lead to an enhancement in the average water temperature. Specifically, a decrease in pitch was associated with an increase in the mean water temperature of approximately 1°C.
Similarly, a judicious reduction in the coil diameter was also observed to contribute to an elevation in the average water temperature by about 1°C.
Furthermore, by concurrently optimizing both the coil pitch and diameter, it was ascertained that the maximum temperature differential along the vertical axis of the water tank could be maintained below 7.50°C. This finding underscores the potential for achieving a more uniform temperature distribution within the tank through careful selection of these geometric parameters.
The insights gleaned from this study furnish valuable guidance for the design optimization of heat pump water heaters, particularly with respect to the configuration of wrap-around condenser coils. The results underscore the efficacy of employing variable-pitch coils and strategically adjusting coil pitch and diameter to enhance thermal performance and achieve more uniform temperature stratification within the water tank.
While this study provides a robust computational framework and compelling simulation results, further experimental validation is warranted to corroborate the findings under real-world operating conditions. Moreover, future investigations should delve into a more comprehensive exploration of the design space, encompassing a wider range of geometric parameters and operating conditions to identify globally optimal coil configurations.
Additionally, future research endeavors could explore the potential benefits of incorporating more advanced coil designs, such as those featuring non-uniform pitch distributions or innovative cross-sectional geometries. Furthermore, the investigation of alternative materials for coil construction, possessing enhanced thermal conductivity or corrosion resistance, could yield further improvements in HPWH performance and longevity.
This computational investigation elucidates the performance characteristics of heat pump water heaters equipped with wrap-around condenser coils, with a particular focus on the comparative evaluation of variable-pitch and constant-pitch configurations. The study underscores the potential for enhancing system performance through the strategic optimization of coil geometry and winding parameters.
The findings of this research hold significant implications for the design and optimization of heat pump water heaters, offering a pathway toward improved energy efficiency, reduced operating costs, and enhanced user comfort. By providing a deeper understanding of the thermal-hydraulic phenomena governing the operation of these systems, this work contributes to the broader objective of advancing sustainable and energy-efficient building technologies. The system performance is enhanced thanks to this research.
Key Takeaways:
In conclusion, this comprehensive numerical investigation has shed light on the intricate interplay between condenser coil geometry, thermal transport phenomena, and overall system performance in heat pump water heaters. The insights derived from this study pave the way for the development of more efficient and effective water heating solutions, contributing to the ongoing pursuit of sustainable and energy-conscious building technologies.
This research investigates the enhancement of airflow dynamics and thermal transfer efficacy in multi-coil condensers through strategic coil arrangement.
This article delves into the common problem of refrigerant leaks in LG split AC units, specifically focusing on the debate between aluminum and copper condenser coils.
This article provides a comprehensive guide on how to effectively clean your air conditioner’s condenser coil.
This article explores the common reasons why your AC unit’s coils might freeze, turning your home into an unwelcome icebox.
This article explains how water chillers work, focusing on the role of water in the cooling process.
This article explores the critical roles of the evaporator coil vs condenser coil in your air conditioner (AC), explaining how they work together to cool your home.
This article dives deep into the costs associated with copper condenser coils in split AC units.
Your air conditioner is a crucial part of your home comfort, especially during hot weather.
This article explores the intricate workings of your home’s HVAC system, focusing on the vital roles of evaporator and condenser coils.
Your air conditioning unit is a complex system with many parts working together to keep your home cool and comfortable.
This article explains how your central air conditioner works, focusing on the critical roles of the evaporator and condenser coils.
This article dives deep into the costs associated with copper condenser coils in split AC units.
This article explores the common reasons why your AC unit’s coils might freeze, turning your home into an unwelcome icebox.
© 2025 Condenser Coil All rights reserved.
Fill out the form below, our team can reply in 20 minutes.