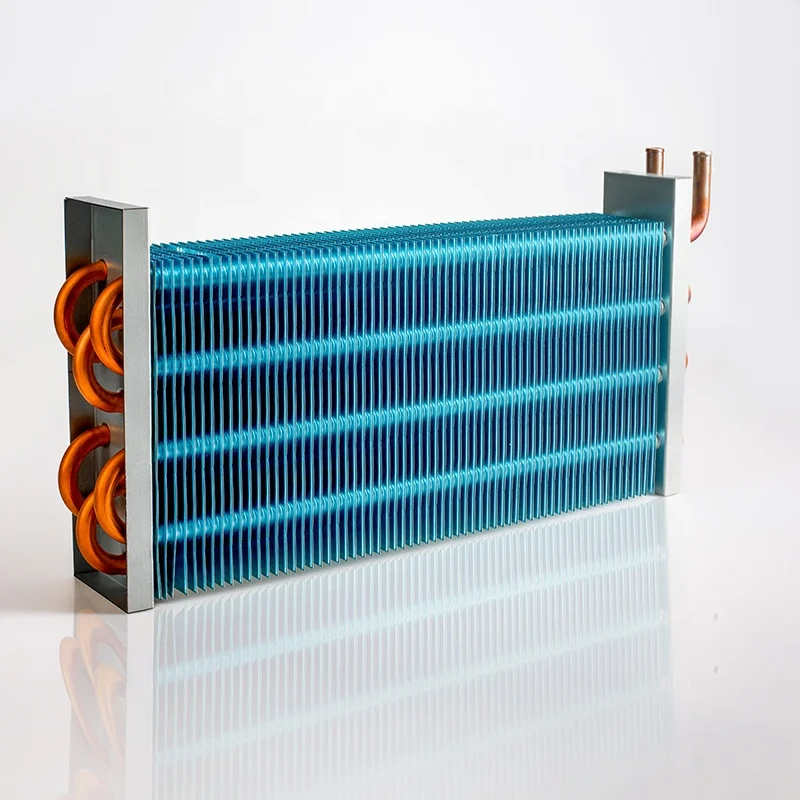
© 2025 Condenser Coil All rights reserved.
This research investigates the enhancement of airflow dynamics and thermal transfer efficacy in multi-coil condensers through strategic coil arrangement. The study reveals that optimizing the spatial configuration of condenser coils can significantly boost performance without necessitating an expansion of the heat transfer surface area. The investigation utilizes a commercially available four-coil condenser from an air-cooled water chiller as the baseline model. By manipulating the included angles between the coils, notable improvements in airflow rates and heat transfer were observed. This was mainly because of the decrease of stagnant zones and the development of uniform flow throughout the heat exchanger. The findings highlight the potential to elevate the performance of air-cooled condensing units by simply adjusting the geometric configuration of the coil arrangements, offering a cost-effective alternative to more complex modifications.
Thermal exchange efficacy is paramount to the energy conservation of air-cooled apparatus, such as air-cooled chillers. Previous research has demonstrated that condenser temperature regulation in air-cooled chillers can lead to substantial energy savings, ranging from approximately 18.2% to 29%. Further experimentation with condenser temperature control under partial load conditions revealed an increase in the chiller’s coefficient of performance (COP) by about 14.5% to 67.2% at reduced ambient air temperatures.
Subsequent investigations into the modulation of condenser fan operation under partial load conditions indicated a marked enhancement in air-cooled chiller performance across varying loads and ambient air temperatures. Moreover, condenser temperature regulation employing inverter-controlled fans was shown to augment energy efficiency by 4.0% to 127.5%. These findings underscore the critical role of condenser temperature management in optimizing the operational efficiency of air-cooled systems.
Numerous studies have delved into the operational parameters of finned-tube heat exchangers. For instance, research on forced-draft air-cooled heat exchangers identified a critical minimum distance for the plenum chamber, beyond which performance is adversely affected. Subsequent studies focusing on the included angle between two finned tube coils demonstrated that reducing the angle from 90° to 45° did not alter the pressure drop; however, a further decrease to 30° resulted in an increased pressure drop across the coils.
Other investigations have concentrated on the specific attributes of finned tube heat exchangers. Experiments involving 15 different plate fin heat exchangers revealed that fin spacing does not significantly impact the heat transfer coefficient. Tube row arrangement was found to have a moderate effect on the friction factor, while fin thickness did not influence either heat transfer or pressure drop. Numerical studies of wavy fins yielded results consistent with experimental data, highlighting the influence of wavy height on friction and heat transfer coefficients.
Multi-coil configurations are commonly employed in air-cooled condensers to achieve compact designs, particularly in air-conditioning units. These condensers typically utilize finned-tube heat exchangers, where fins are added to the tubes to increase the effective heat transfer surface area. However, such compact arrangements often suffer from airflow maldistribution, which negatively impacts heat transfer performance. This study addresses this issue by investigating the effects of varying the included angle (θ) between the inner coil (coil 1) and the outer coil (coil 2) of a typical multi-coil condenser.
The maldistribution of airflow can significantly hinder the overall efficiency of the heat exchanger. Uneven airflow leads to suboptimal utilization of the heat transfer surface, with certain areas of the coils experiencing reduced flow and, consequently, diminished heat transfer rates. By optimizing the included angle between the coils, it is possible to achieve a more uniform flow distribution, thereby maximizing the utilization of the available heat transfer area and enhancing the overall performance of the condenser. This is very important in heating and air conditioning.
To investigate the impact of different coil configurations on airflow distribution and heat transfer, a three-dimensional (3-D) computational model was developed to simulate the four-coil heat exchangers of an air-cooled chiller condenser. The physical model, as depicted in the provided figures, consists of three bays of four-coil heat exchangers, each with identical dimensions. The computational model incorporates the characteristic curves for the condenser fans and the pressure drop characteristics across the coils, derived from a commercially available air-cooled water chiller.
The computational model employs a finite volume method to solve the governing equations for fluid flow and heat transfer. The model assumes steady-state operation and neglects the effects of radiation. The boundary conditions for the model include the inlet air temperature and the refrigerant temperature within the coils. The fan performance curve is incorporated into the model to accurately simulate the airflow generated by the condenser fans.
In the thermal transfer analysis, the coils are conceptually partitioned into multiple horizontal segments, denoted as A, B, C, and D, as illustrated in the accompanying diagram. These horizontal segments are further subdivided into distinct regions. Average air velocity was computed for each of these regions within the computational simulation. Subsequently, these average air velocity values were employed to ascertain the heat transfer coefficient for the corresponding regions on the coils.
The thermal transfer for each of these regions can then be computed, and the aggregate heat dissipation is determined by summing the contributions from all regions. This detailed approach allows for a comprehensive assessment of the heat transfer performance across the entire coil surface. This helps in the assessment of condenser coils work together.
Empirical validation of the computed airflow distribution was performed utilizing an air-cooled chiller with a nominal capacity of 125 USRT (United States Refrigeration Tons). The condenser comprised three bays of flat plate finned tube heat exchangers arranged in a configuration consistent with the computational model. Each bay of the condenser was equipped with four fans, the characteristics of which are depicted in the provided figures. The external condenser was vertically oriented and had a specific included angle, θ.
Air velocity measurements were taken at various locations across the coil surfaces using a hot-wire anemometer. The measured air velocity data were then compared with the corresponding values obtained from the CFD simulation. The close agreement between the experimental and simulated results validated the accuracy of the computational model. Experimental verification is needed in technological and scientific studies.
The results of the air velocity distribution for the baseline configuration (representing an actual condenser) in the central cross-sectional plane are presented in the relevant figure. The analysis reveals a non-uniform air velocity profile across the coil surface. The outer coil (coil 1) experiences a greater airflow volume, and air velocity is generally elevated at the upper extremities of the coils. Conversely, the lower coil exhibits reduced flow velocity, rendering the lower portion of the coil less efficacious.
Further analysis across different coil configurations demonstrates that altering the included angle between the coils significantly influences the airflow distribution. By optimizing the included angle, it is possible to mitigate the maldistribution of airflow, leading to a more uniform flow pattern across the coil surfaces. This, in turn, enhances the overall heat transfer performance of the condenser.
Modifying the configuration of the included angles within the multi-coil condenser arrangement has been found to exert a substantial influence on airflow patterns and, consequently, on thermal transfer efficacy. Specifically, it was ascertained that altering the included angle can yield an augmentation in airflow rate of up to 7.85% when juxtaposed with a commercially available multi-coil condenser. This is an important discovery in heating and air conditioning units.
This enhancement in airflow corresponds to a 5.29% elevation in heat transfer. These advancements are primarily attributed to the diminution of stagnant flow zones within the heat exchanger coils and the attainment of a more uniform flow distribution across the coils. Such findings underscore the potential for optimizing condenser performance through strategic adjustments to coil geometry, thereby maximizing heat transfer efficiency while minimizing energy consumption.
A comparative analysis of five different coil configurations, each with a unique included angle (θ), was conducted to assess their impact on airflow distribution and heat transfer performance. Cases 1 through 5 correspond to included angles of approximately 40.5°, 43.5°, 45.4°, 46.6°, and 47.1°, respectively.
The results of the analysis indicate that Case 3, with an included angle of approximately 45.4°, exhibits the most favorable performance in terms of both airflow distribution and heat transfer. This configuration minimizes the stagnant flow regions and promotes a more uniform flow across the coil surfaces, leading to a significant improvement in overall condenser efficiency.
This investigation has demonstrated that strategic modification of the included angles within compact multi-coil condensers can effectively mitigate airflow maldistribution and consequently enhance thermal transfer performance. The findings reveal that adjusting the configuration of the coils can significantly impact airflow patterns and, by extension, the overall efficiency of the condenser. Specifically, it was observed that an optimal included angle exists, which minimizes stagnant flow zones and promotes a more uniform distribution of airflow across the coil surfaces.
These insights hold substantial implications for the design and optimization of air-cooled condensing units. By simply altering the geometric arrangement of the coils, it is possible to achieve notable improvements in performance without resorting to costly modifications such as increasing the heat transfer surface area or upgrading fan systems. Future research endeavors should focus on exploring a wider range of coil configurations and operating conditions to further refine the understanding of the relationship between coil geometry, airflow dynamics, and thermal transfer efficacy.
Key Takeaways:
The escalating global energy demand, coupled with a growing awareness of environmental sustainability.
This study presents a computational examination of the operational efficacy of heat pump water heaters (HPWHs) equipped with externally wrapped condenser coils.
This article explains how water chillers work, focusing on the role of water in the cooling process.
This document details a study on the application of multi-objective evolutionary algorithms, specifically Genetic Algorithms (GAs).
This research investigates the enhancement of airflow dynamics and thermal transfer efficacy in multi-coil condensers through strategic coil arrangement.
This document elucidates the principal factors influencing thermal exchange between the refrigerant and the airstream within a plate finned-tube heat exchanger
This article explores the intricate workings of your home’s HVAC system, focusing on the vital roles of evaporator and condenser coils.
This step-by-step guide provides product help for homeowners looking to maintain their air conditioning system by cleaning the condenser coils.
Your air conditioner is a crucial part of your home comfort, especially during hot weather.
This numerical investigation delves into the influence of geometric parameters of immersed helical condenser coils.
Your air conditioning unit is a complex system with many parts working together to keep your home cool and comfortable.
This article explains how your central air conditioner works, focusing on the critical roles of the evaporator and condenser coils.
This research investigates the enhancement of airflow dynamics and thermal transfer efficacy in multi-coil condensers through strategic coil arrangement.
© 2025 Condenser Coil All rights reserved.
Fill out the form below, our team can reply in 20 minutes.