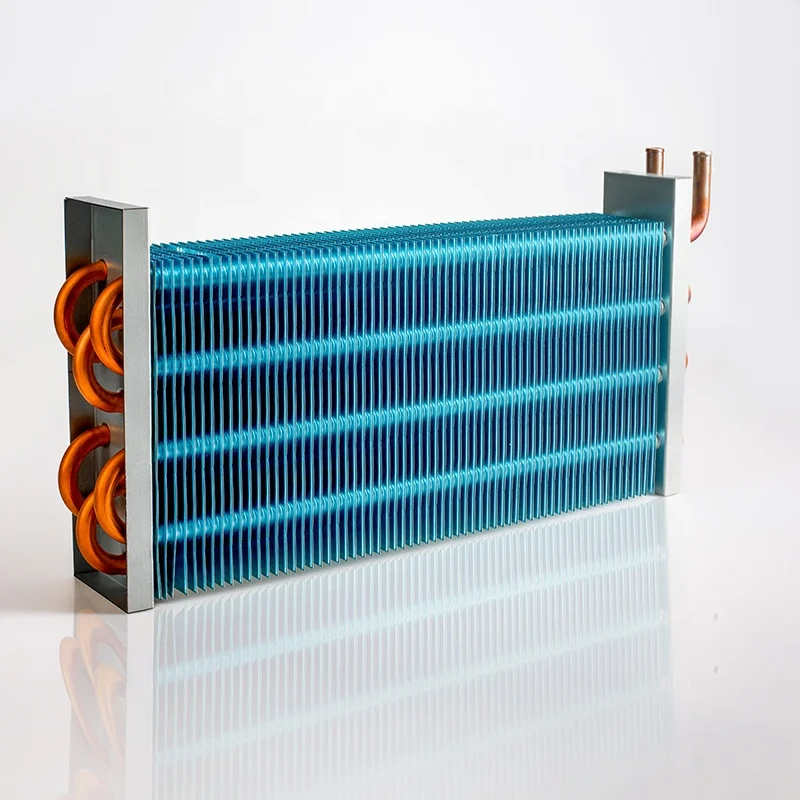
© 2025 Condenser Coil All rights reserved.
This document details a study on the application of multi-objective evolutionary algorithms, specifically Genetic Algorithms (GAs), to optimize the design of air-cooled condenser coils. The optimization problem focuses on two primary objectives: maximizing heat rejection capacity and minimizing manufacturing costs. Air-cooled heat exchangers, particularly condenser coils, are crucial components in refrigeration and air-conditioning systems. The design process is complex due to the interplay between performance parameters (e.g., tube length, fin type, airflow rate) and economic factors (e.g., material cost, fan assembly cost). This research leverages a sophisticated condenser simulation model coupled with a multi-objective GA to generate a set of Pareto-optimal solutions, offering designers a range of optimal trade-offs between performance and cost.
Heat exchangers are devices engineered to facilitate thermal energy transfer between two or more fluids at differing temperatures. In the realm of refrigeration and air conditioning, air-cooled condensers are pivotal, serving to reject heat absorbed by the refrigerant in the evaporator to the ambient environment. The efficiency of this heat transfer process is paramount to the overall system performance.
The thermal performance of a condenser coil is contingent upon a multitude of design variables. These include geometric parameters such as tube length, tube diameter, fin density, fin height, and the number of parallel refrigerant circuits. Additionally, operational parameters like refrigerant flow rate, inlet conditions, air flow rate, and fan power significantly influence the heat rejection capacity.
The economic viability of a condenser design is intrinsically linked to its material and manufacturing costs. The selection of materials for tubes and fins, the complexity of the fin structure, the number of fans employed, and the overall dimensions of the coil all contribute to the final production cost.
Optimizing condenser coil design is inherently a multi-objective problem. Designers must strive to achieve maximal heat rejection while simultaneously minimizing manufacturing costs. These objectives often conflict, necessitating a trade-off analysis to identify the most suitable design solutions.
Historically, various optimization methodologies have been applied to heat exchanger design. These include techniques based on Lagrange multipliers, aimed at optimizing effectiveness for a given pressure ratio in gas turbine regenerators. Other methods, such as augmented Lagrangian multipliers, have been coupled with simulation programs to perform constrained single-objective optimizations, such as minimizing volume for a given heat transfer rate.
Simulated annealing has been utilized for constrained single-objective optimization, targeting the minimization of heat transfer area and purchase costs. This method draws inspiration from the annealing process in metallurgy, gradually reducing the system’s “temperature” to converge towards an optimal solution.
Genetic algorithms (GAs) made their debut in heat exchanger optimization in the late 1990s. Early studies demonstrated the successful application of GAs in optimizing heat exchangers using simplified “black box” models. These investigations highlighted the capability of GAs to yield multiple solutions of comparable quality, thereby granting designers more flexibility.
Evolutionary algorithms (EAs) have witnessed substantial advancements in recent years. Researchers have developed various specialized EAs for multi-objective optimization, classifying them into Pareto-based and non-Pareto-based approaches. Notable contributions in this field provide comprehensive overviews of EAs and their applications to diverse engineering problems.
MOGAs are a class of search algorithms inspired by the principles of natural evolution. They emulate the process of natural selection, where individuals with advantageous traits are more likely to reproduce and pass on their genes to the next generation. In the context of optimization, these “individuals” represent candidate solutions, and their “traits” correspond to design variables.
MOGAs maintain a population of candidate solutions, evaluating each based on its performance concerning the defined objectives. A fitness value, which may or may not directly correspond to the objective function value, is assigned to each solution, reflecting its overall desirability. Solutions with higher fitness are preferentially selected for reproduction.
The reproduction process in MOGAs involves genetic operators such as crossover and mutation. Crossover combines the “genetic material” (design variables) of two parent solutions to create offspring, while mutation introduces random variations into the offspring’s “genes.” These operators facilitate exploration of the design space and the discovery of novel solutions.
MOGAs are particularly well-suited for handling multi-objective optimization problems, where multiple conflicting objectives must be considered simultaneously. They employ concepts like dominance and Pareto optimality to navigate the trade-offs between objectives. Additionally, MOGAs can incorporate constraints, ensuring that the generated solutions adhere to specified design limitations.
The multi-objective optimization task at hand can be formally expressed in mathematical terms. The objective is to minimize or maximize a set of objective functions, denoted as fm(x), where x represents the vector of n decision variables. These objective functions are subject to inequality and equality constraints, represented by gj(x) and hk(x), respectively. Furthermore, domain constraints restrict each decision variable xi to lie within a specified range [xiL, xiU].
In multi-objective optimization, the concept of dominance plays a crucial role. A solution x(1) is said to dominate another solution x(2) in a minimization context if it is no worse than x(2) in all objectives and strictly better than x(2) in at least one objective.
A non-dominated set is a collection of solutions where none of the solutions are dominated by any other member of the set. When this set encompasses the entire solution space, it is referred to as the Pareto-optimal set. The goal of a multi-objective optimization algorithm is to identify solutions that are as close as possible to the Pareto-optimal set while maintaining diversity among the solutions.
Since GAs typically operate with scalar fitness values, aggregating methods or utility functions are commonly used to assign fitness in multi-objective scenarios. Two fitness assignment schemes are employed in this research: MOGA1 (Non-dominated Sorting GA) and MOGA2. MOGA1 ranks solutions based on non-dominated sorting, ensuring that solutions within the same non-dominated set have equal fitness. MOGA2 assigns fitness based on the number of solutions that dominate a particular solution.
The economic objective of this optimization study is to minimize the total cost of the condenser coil. The cost is modeled as a function of several factors, including the number of tubes, fins per inch (FPI), number of fans, and the overall dimensions (width and height) of the coil.
The performance objective is to maximize the heat rejection capacity of the condenser coil. For a given refrigerant mass flow rate, the aim is to achieve the highest possible heat transfer from the refrigerant to the ambient air.
The optimization process is subject to several constraints: Refrigerant-side pressure drop: The pressure drop experienced by the refrigerant as it flows through the condenser coil must remain within specified limits. Fan width vs. tube length: The combined width of the fans mounted on the condenser cabinet must not exceed the length of the tubes. Coil height: The overall height of the coil is restricted to a maximum allowable value. Tube length: The chosen tube length must be less than or equal to the current tube length used in the existing design. Air-side pressure drop: The pressure drop of the air flowing across the coil must match the pressure head supplied by the fans. Domain constraints: All independent variables must fall within their respective lower and upper bounds.
Tube length is treated as a continuous variable, meaning it can take any value within a specified range. The optimization algorithm explores different tube lengths to find the optimal balance between heat transfer area and cost.
Tube outer diameter is a discrete variable, meaning it can only assume specific predefined values. In this study, four different tube sizes are considered.
The number of parallel refrigerant circuits is another discrete variable. The optimization algorithm evaluates different circuit configurations to determine the most efficient arrangement for heat transfer.
Fin density, expressed as fins per inch (FPI), is a discrete variable that can range from 6 to 16. Higher fin density generally leads to increased heat transfer but can also result in higher air-side pressure drop and increased cost.
The choice of fan model is a discrete variable. Twenty different fan models are available, each with its own performance characteristics (pressure drop vs. flow rate) and cost.
The number of fans used in the condenser is a discrete variable, ranging from 8 to 12 in multiples of 2. The optimization algorithm determines the optimal number of fans to achieve the desired airflow rate while minimizing cost.
This research employs a multi-objective genetic algorithm (MOGA) based on the work of Narayanan and Azarm (1999). The implementation includes two fitness assignment schemes: MOGA1 and MOGA2. Key algorithm parameters include a population size of 100, a crossover probability of 0.9, a mutation probability of 0.05, and a termination criterion based on the maximum number of iterations.
A binary Gray encoding scheme is used to represent the design variables. Each variable is assigned a specific number of bits: tube length (10 bits), number of parallel circuits (2 bits), tube diameter (2 bits), fan ID (5 bits), FPI (4 bits), and number of fans (2 bits).
Table 1: String representation and related parameters
Parameter | Encoding | Bits | Possible Values |
---|---|---|---|
Tube Length | Binary | 10 | Continuous |
Parallel Circuits | Binary | 2 | 4 |
Tube Diameter | Binary | 2 | 4 |
Fan ID | Binary | 5 | 20 |
FPI | Binary | 4 | 6-16 |
Number of Fans | Binary | 2 | 8, 10, 12 |
Before evaluating the objective functions and constraints, the binary strings are decoded to obtain the actual values of the design variables. Constraints are handled both within and outside the optimization algorithm. The refrigerant-side pressure drop and fan width vs. tube length constraints are checked during the evaluation of each candidate solution, while the air-side pressure drop constraint is handled iteratively by adjusting the airflow rate until the fan pressure matches the coil pressure drop.
The condenser simulation model employed in this study is based on the work of Jiang et al. (2002). It utilizes a segmented modeling approach, dividing each tube into multiple segments to account for variations in airflow distribution and refrigerant properties along the tube length.
The model incorporates a two-dimensional airflow simulation capability, allowing for variations in air velocity along the height of the condenser coil. This feature is crucial for accurately predicting the performance of coils with non-uniform airflow patterns.
The simulation model offers a high degree of flexibility, allowing users to modify various parameters, including coil dimensions, number of tubes, fan type, fin density, and air-side conditions (velocity, humidity, temperature).
The condenser model has been validated against experimental data to ensure its accuracy. The model was adjusted by modifying correction factors for air and refrigerant-side heat transfer and pressure drop correlations until the predicted outlet subcooling and heat rejection capacity matched the experimental values within ±1K and ±4%, respectively.
The optimization process involves an iterative loop where the genetic algorithm generates a population of candidate solutions, the condenser simulation model evaluates each solution’s performance and cost, and the GA then uses this information to create a new generation of solutions. This cycle continues until the termination criterion (maximum number of iterations) is met.
During each iteration, the condenser model is executed for each candidate solution. This involves first iterating to find a matching airflow rate that satisfies the air-side pressure drop constraint and then solving for the refrigerant pressures and temperatures throughout the coil. The model outputs the heat rejection capacity, refrigerant-side pressure drop, and total cost for each solution.
The optimization algorithm was executed multiple times with different fitness ranking schemes (MOGA1 and MOGA2) and varying numbers of iterations (250 and 500). The results are summarized in Table 2, which presents key metrics such as the number of function calls, CPU time, number of infeasible solutions, number of Pareto solutions, and average values of the objective functions.
Table 2: Optimization Results for Different Schemes
Parameter | MOGA1-250 | MOGA1-500 | MOGA2-250 | MOGA2-500 |
---|---|---|---|---|
Max. Iterations | 250 | 500 | 250 | 500 |
Function Calls | 2610 | 5110 | 2610 | 5110 |
CPU Time (seconds) | 91411 | 165757 | 101531 | 173111 |
Infeasible Solutions | 636 | 1367 | 672 | 1234 |
Pareto Solutions | 93 | 92 | 94 | 92 |
Better Solution Count | 20 | 44 | 36 | 48 |
Avg. Objective 1 | 1.0674 | 1.0745 | 1.0744 | 1.0686 |
Avg. Objective 2 | 0.9 | 0.909 | 0.902 | 0.896 |
The results indicate that the optimization process requires significant computational resources due to the detailed nature of the condenser simulation model. Increasing the number of iterations generally leads to a higher number of “better” solutions (those that dominate the baseline design in both objectives) but may also result in a decrease in the total number of Pareto solutions. The quality of the Pareto front, as measured by the overall Pareto spread, varies depending on the algorithm and parameters used.
This study demonstrates the effectiveness of multi-objective genetic algorithms (MOGAs) in optimizing the design of air-cooled condenser coils. MOGAs successfully generate a diverse set of Pareto-optimal solutions, providing designers with a range of trade-offs between heat rejection capacity and manufacturing cost.
The use of a detailed condenser simulation model is crucial for accurately predicting the performance of different design configurations. The model’s ability to account for variations in airflow and refrigerant properties allows for a more realistic assessment of the coil’s behavior.
The optimization process can be computationally intensive, particularly when using detailed simulation models. However, the benefits of obtaining a set of optimal design options often outweigh the computational cost.
Future research could explore the incorporation of additional design objectives, such as minimizing refrigerant charge or optimizing for specific operating conditions. Additionally, investigating alternative optimization algorithms or hybrid approaches could potentially lead to further improvements in efficiency and solution quality.
In conclusion, this research showcases the power of combining sophisticated simulation models with multi-objective evolutionary algorithms to address complex engineering design problems. The application of MOGAs to condenser coil optimization provides valuable insights into the trade-offs between performance and cost, empowering designers to make informed decisions and develop more efficient and cost-effective refrigeration and air-conditioning systems. The generated Pareto-optimal solutions offer a spectrum of design choices, each representing a different balance between maximizing heat rejection and minimizing manufacturing expenses. This flexibility is invaluable in the design process, allowing engineers to select the solution that best aligns with specific project requirements and constraints.
Your air conditioning unit is a complex system with many parts working together to keep your home cool and comfortable.
The escalating global energy demand, coupled with a growing awareness of environmental sustainability.
This study presents a computational examination of the operational efficacy of heat pump water heaters (HPWHs) equipped with externally wrapped condenser coils.
This article explores the critical roles of the evaporator coil vs condenser coil in your air conditioner (AC), explaining how they work together to cool your home.
This article provides a comprehensive guide on how to effectively clean your air conditioner’s condenser coil.
This article provides a comprehensive guide on how to effectively clean your refrigerator’s condenser coils.
This document details a study on the application of multi-objective evolutionary algorithms, specifically Genetic Algorithms (GAs).
This document elucidates the principal factors influencing thermal exchange between the refrigerant and the airstream within a plate finned-tube heat exchanger
This article dives deep into the world of condenser coils, a crucial component of any HVAC system, exploring their function, design, and key features.
Your air conditioner is a lifesaver during hot summer months, providing welcome relief from the heat.
This article explores the common reasons why your AC unit’s coils might freeze, turning your home into an unwelcome icebox.
The escalating global energy demand, coupled with a growing awareness of environmental sustainability.
This step-by-step guide provides product help for homeowners looking to maintain their air conditioning system by cleaning the condenser coils.
© 2025 Condenser Coil All rights reserved.
Fill out the form below, our team can reply in 20 minutes.