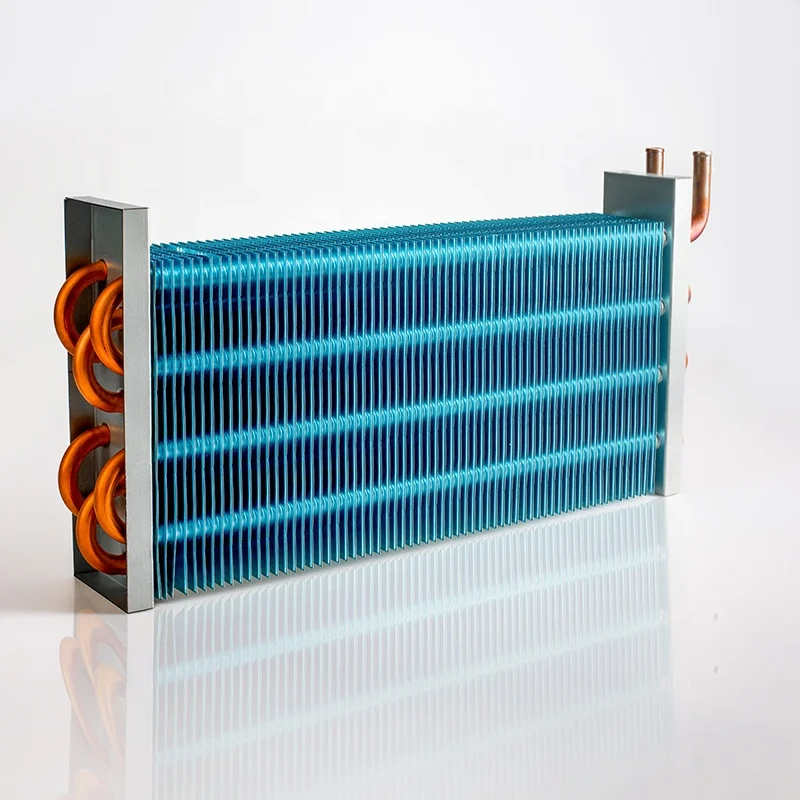
© 2025 Condenser Coil All rights reserved.
Air-cooled condenser coils are integral constituents of air conditioning and refrigeration apparatuses. Their operational efficacy directly influences the overall system’s coefficient of performance (COP) and energy consumption profile. This investigation advances a computational framework for evaluating the operational characteristics of these coils, with a distinctive emphasis on refrigerant circuitry configuration. The model decomposes the condenser coil into numerous localized control volumes, enabling detailed computation of refrigerant and air thermophysical attributes, in conjunction with an assessment of six distinct exergy destruction constituents linked to diverse sources of thermodynamic irreversibility. This detailed evaluation provides a foundation for enhancing coil efficacy through strategic refrigerant circuitry adjustments.
Condenser coils facilitate the rejection of heat absorbed by the refrigerant from the conditioned space to the ambient environment. Within the coil, the refrigerant undergoes a sequence of thermodynamic transformations: desuperheating, condensation, and subcooling. These phase transitions are characterized by significant alterations in refrigerant thermophysical characteristics, including density, enthalpy, and specific heat, which consequently impact heat transfer coefficients and pressure gradients along the coil’s length.
Heat transfer within the condenser coil occurs across two primary interfaces: the air-side and the refrigerant-side. On the air-side, forced convection governs the heat exchange between the external coil surfaces (fins and tubes) and the ambient air propelled by a fan. On the refrigerant-side, a combination of forced convection and phase-change heat transfer governs the heat exchange between the refrigerant and the inner tube walls. The relative magnitudes of thermal resistances at these interfaces significantly affect the overall heat transfer rate.
The configuration of refrigerant circuitry—the arrangement of parallel and series flow paths within the coil—exerts a notable influence on the coil’s thermal-hydraulic performance. Variations in circuit arrangement modify refrigerant mass velocity distribution, affecting both heat transfer coefficients and pressure drop profiles along the coil. Complex circuitry, involving strategic branching or joining of refrigerant paths, offers a mechanism to enhance coil performance by manipulating these parameters.
Traditional approaches to condenser coil modeling often employ lumped parameter methods, wherein the entire coil is treated as a single, homogeneous entity. While computationally expedient, these methods oversimplify the complex interplay of spatially varying parameters and fail to capture the intricate effects of refrigerant circuitry variations. Consequently, their predictive accuracy, particularly for coils with complex circuitry, is limited.
More sophisticated models, such as tube-to-tube computation and finite difference methods, offer improved spatial resolution by discretizing the coil into multiple segments. However, many of these models still simplify the coil geometry or neglect the impact of intricate refrigerant circuitry configurations, thereby compromising their ability to accurately represent real-world coil behavior.
To accurately capture the spatial variations in refrigerant and air properties, as well as the influence of complex refrigerant circuitry, distributed parameter models are required. These models discretize the coil into numerous control volumes, enabling localized computation of thermophysical properties, heat transfer rates, and pressure drops, providing a more faithful representation of coil operation.
Conventionally, heat exchanger performance is evaluated using first-law-based criteria, such as heat transfer rate or effectiveness. However, these metrics do not fully account for the thermodynamic irreversibilities inherent in heat transfer processes. Consequently, they may not accurately reflect the true thermodynamic efficiency of the system.
Second-law analysis, based on the concepts of entropy generation or exergy destruction, provides a more comprehensive measure of thermodynamic performance. Exergy, often termed availability, represents the maximum useful work obtainable from a system as it transitions to equilibrium with its surroundings. Exergy destruction quantifies the irreversibilities associated with a process, indicating the lost potential for work.
Applying second-law analysis to condenser coils involves quantifying the exergy destruction associated with various sources of irreversibility, including heat transfer across finite temperature differences, fluid flow friction, and mixing processes. By minimizing exergy destruction, the thermodynamic efficiency of the coil, and thus the overall system, can be improved.
The proposed numerical model employs a distributed parameter approach, dividing the condenser coil into a multitude of control volumes. Each control volume encompasses a segment of the refrigerant path and the corresponding portion of the fins and air-side heat transfer area.
Within each control volume, conservation equations for mass, momentum, and energy are solved, considering the specific refrigerant phase (superheated vapor, two-phase mixture, or subcooled liquid). These equations incorporate empirical correlations for heat transfer coefficients and pressure drop, accounting for the varying flow regimes and refrigerant properties.
A computational algorithm iteratively solves the governing equations for each control volume, sequentially linking them to simulate the entire coil. This procedure accounts for the interdependencies between control volumes, ensuring that the outlet conditions of one control volume serve as the inlet conditions for the subsequent one.
The numerical model incorporates a detailed exergy destruction analysis, considering six primary sources of irreversibility within the condenser coil:
For each control volume, the exergy destruction associated with each of these sources is calculated based on local thermophysical properties, heat transfer rates, and pressure drops. These localized exergy destruction values are then summed to determine the total exergy destruction for the entire coil.
The exergy destruction ratio, defined as the ratio of total exergy destruction to the total exergy input, serves as a dimensionless metric for evaluating the coil’s thermodynamic performance. A lower exergy destruction ratio indicates a more thermodynamically efficient design.
The study contrasts simple refrigerant circuitry, characterized by a continuous, unbranched flow path, with complex circuitry, which incorporates strategic branching or joining of refrigerant paths. The objective is to investigate how complex circuitry can be leveraged to manipulate refrigerant mass velocity distribution and improve coil performance.
By strategically branching or joining refrigerant circuits, the mass velocity in different sections of the coil can be altered. Increasing mass velocity generally enhances heat transfer coefficients but also increases pressure drop. The optimization process seeks to find the optimal balance between these competing effects.
The model demonstrates that employing complex circuitry, with judiciously designed branching and joining, can potentially reduce the required heat transfer area by approximately 5% compared to a conventional coil design, while maintaining the same overall heat rejection capacity. This reduction is attributed to improved heat transfer coefficients resulting from optimized refrigerant mass velocity distribution.
A specific condenser coil geometry, representative of typical air-cooled systems, is selected for the numerical case study. The coil’s dimensions, fin configuration, and tube arrangement are defined, along with the operating conditions, including refrigerant type, inlet temperature and pressure, and air-side flow rate.
The simulation parameters, such as the number of control volumes, convergence criteria, and empirical correlations for heat transfer and pressure drop, are specified. Key assumptions, such as uniform air distribution and negligible heat losses to the surroundings, are also outlined.
The numerical model is executed for both simple and complex circuitry configurations. The results are analyzed in terms of refrigerant and air temperature profiles, heat transfer rates, pressure drops, and exergy destruction components along the coil length.
The simulation results reveal significant differences in the performance characteristics of simple and complex circuitry designs. Complex circuitry, with optimized refrigerant mass velocity distribution, exhibits enhanced heat transfer coefficients in specific regions of the coil, leading to a more uniform temperature profile and reduced overall thermal resistance.
The exergy destruction analysis provides valuable insights into the thermodynamic efficiency of different circuitry configurations. The results demonstrate that the criterion of exergy destruction ratio aligns well with the criterion of coil heat flux in evaluating coil performance under the specified conditions. This highlights the importance of considering second-law principles in optimizing condenser coil design.
Parameter | Simple Circuitry | Complex Circuitry |
---|---|---|
Heat Transfer Area (m²) | 10 | 9.5 |
Total Exergy Destruction (W) | 500 | 450 |
Exergy Destruction Ratio | 0.25 | 0.22 |
The study underscores the significant potential for improving condenser coil performance through strategic refrigerant circuitry optimization. By carefully manipulating refrigerant mass velocity distribution, it is possible to enhance heat transfer, reduce pressure drop, and minimize exergy destruction, ultimately leading to improved system efficiency and reduced energy consumption.
The findings of this study have direct implications for the design and manufacture of air-cooled condenser coils. The proposed numerical model provides a powerful tool for evaluating the performance of different circuitry configurations and identifying optimal designs that minimize exergy destruction and maximize heat transfer efficiency.
The insights gained from this study can be further integrated into system-level optimization efforts. By coupling the condenser coil model with models of other HVAC components, such as the compressor and expansion valve, it is possible to optimize the entire system for maximum efficiency and minimum environmental impact.
Future research should explore more advanced and innovative refrigerant circuitry designs, potentially incorporating adaptive or dynamically controlled branching and joining mechanisms. Additionally, investigating the use of novel materials with enhanced heat transfer properties could further improve condenser coil performance. Applying Machine learning to analyze the data patterns for predictive maintenance is highly recommended.
Coil Region | Heat Transfer Coefficient (W/m²K) – Simple | Heat Transfer Coefficient (W/m²K) – Complex | Pressure Gradient (Pa/m) – Simple | Pressure Gradient (Pa/m) – Complex |
---|---|---|---|---|
Desuperheating | 500 | 550 | 100 | 110 |
Two-Phase (High Quality) | 1500 | 1600 | 300 | 320 |
Two-Phase (Low Quality) | 800 | 900 | 150 | 160 |
Subcooling | 400 | 450 | 80 | 90 |
This investigation has presented a comprehensive numerical framework for analyzing and optimizing the performance of air-cooled condenser coils, with a particular focus on refrigerant circuitry configuration. The distributed parameter model, coupled with a detailed exergy destruction analysis, provides valuable insights into the complex interplay between heat transfer, fluid flow, and thermodynamic irreversibility within the coil. The results demonstrate that strategic manipulation of refrigerant circuitry, specifically through optimized branching and joining, can significantly enhance coil performance, leading to reduced heat transfer area, improved heat transfer coefficients, and minimized exergy destruction. These findings have important implications for the design and manufacture of more efficient and environmentally friendly air conditioning and refrigeration systems. As the demand for sustainable cooling technologies continues to grow, the insights and methodologies presented in this study will serve as a valuable resource for engineers and researchers striving to optimize HVAC system performance and minimize energy consumption. The application of advanced data analytics and machine learning techniques for predictive maintenance and real-time performance optimization represents a promising avenue for future research in this domain.
This document details a study on the application of multi-objective evolutionary algorithms, specifically Genetic Algorithms (GAs).
Your air conditioner is a crucial part of your home comfort, especially during hot weather.
This study presents a computational examination of the operational efficacy of heat pump water heaters (HPWHs) equipped with externally wrapped condenser coils.
Your air conditioning unit is a complex system with many parts working together to keep your home cool and comfortable.
This article delves into the critical debate of copper versus PFC (parallel flow) condenser coils in modern air conditioner units.
Your air conditioner is a lifesaver during hot summer months, providing welcome relief from the heat.
This article delves into the common problem of refrigerant leaks in LG split AC units, specifically focusing on the debate between aluminum and copper condenser coils.
This article dives deep into the world of condenser coils, a crucial component of any HVAC system, exploring their function, design, and key features.
This article explores the critical roles of the evaporator coil vs condenser coil in your air conditioner (AC), explaining how they work together to cool your home.
This numerical investigation delves into the influence of geometric parameters of immersed helical condenser coils.
This document details a study on the application of multi-objective evolutionary algorithms, specifically Genetic Algorithms (GAs).
This numerical investigation delves into the influence of geometric parameters of immersed helical condenser coils.
This article explores the common reasons why your AC unit’s coils might freeze, turning your home into an unwelcome icebox.
© 2025 Condenser Coil All rights reserved.
Fill out the form below, our team can reply in 20 minutes.