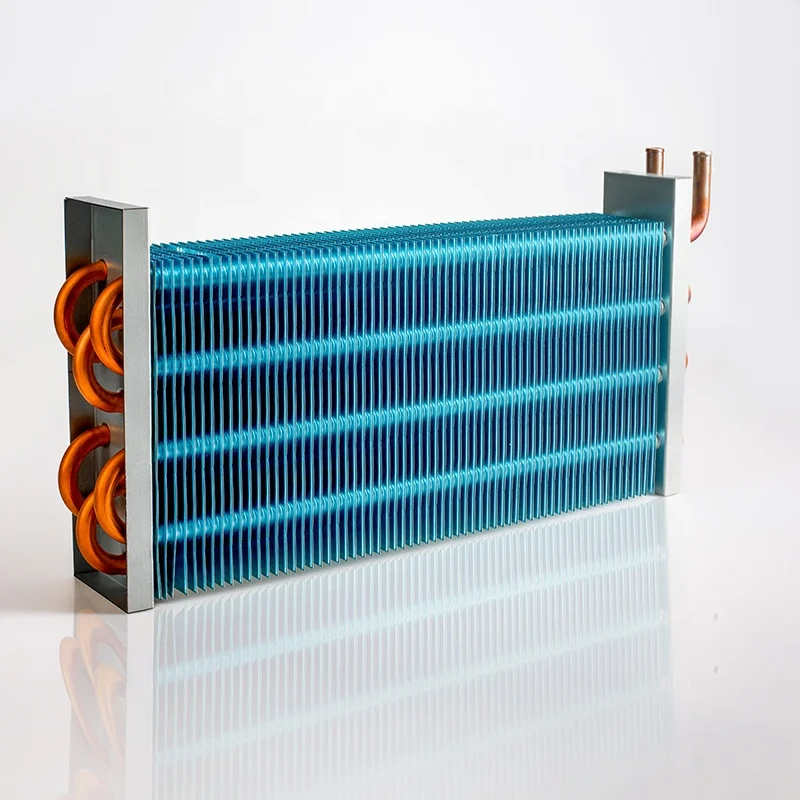
© 2025 Condenser Coil All rights reserved.
This document elucidates the principal factors influencing thermal exchange between the refrigerant and the airstream within a plate finned-tube heat exchanger, commonly referred to as an evaporator or condenser coil in air conditioning (AC) systems. The primary considerations explored encompass the internal heat transfer coefficient, the thermal contact resistance manifested between the fin and the tube, and the external heat transfer coefficient. Empirical correlations are delineated to facilitate the quantification of heat transfer rates associated with each of these factors. Furthermore, supplementary design aspects pertinent to these three thermal transfer mechanisms are presented and deliberated upon. The discussion extends to encompass in-tube augmentation, the ramifications of oil-refrigerant mixtures, and the phenomenon of frosting, given their consequential impact on heat transfer within the coil. Additionally, methodologies for tube circuit configuration and the prevailing standards for coil performance rating are outlined.
A representative vapor-compression cycle inherent to air conditioning systems is illustrated in Figure 1. The fundamental constituents depicted in this schematic are ubiquitous across various system configurations. Notably, the expansion valve and accumulator represent relatively uncomplicated and cost-effective components. Consequently, the evaporator and condenser, in conjunction with the compressor, constitute the primary elements of the system in terms of capital expenditure, spatial footprint, and the potential to influence operational expenses—specifically, compressor power consumption—via judicious design choices.
Figure 1 additionally features a pressure-enthalpy diagram delineating both idealized and actual vapor-compression cycles. The numerical annotations on this diagram denote the thermodynamic state of the refrigerant as it traverses the evaporator and condenser. In particular, a saturated mixture ingresses the evaporator (point 4), and superheated vapor egresses (point 1a). Conversely, for the condenser, superheated vapor enters (point 2a), and subcooled liquid exits (point 3).
Furthermore, Figure 1 underscores the differential pressure and temperature regimes characterizing condenser and evaporator operation. Condensers function under elevated pressures and temperatures, whereas evaporators operate at comparatively diminished pressures and temperatures.
The prevalent configuration for air conditioning evaporators and condensers is the air-to-refrigerant heat exchanger typology. Predominantly, airflow is directed across a circular tube bank augmented with continuous plate fins, as depicted in Figure 2. This structural arrangement lends the nomenclature “plate finned-tube heat exchanger.” The evaporating or condensing refrigerant circulates through tubes oriented perpendicularly to the airflow, arrayed in staggered rows.
The end views presented in Figure 2 reveal the interconnectivity of the tubes, enabling their coiling to achieve diverse configurations of passes, rows, and parallel flow paths. This characteristic justifies the appellation “evaporator and condenser coil.” Typically, the fins are fabricated from aluminum, while the tubes are constructed from copper. However, instances exist where both constituents are manufactured from a homogeneous material. The fins are affixed to the tubes by inserting the tubes into apertures stamped into the fins and subsequently expanding the tubes via mechanical or hydraulic processes.
The design of evaporator and condenser coils is fraught with complexities, a principal one being their inapplicability to conventional heat exchanger analysis methodologies, such as the Logarithmic Mean Temperature Difference (LMTD) and effectiveness-Number of Transfer Units (NTU) methods. This limitation stems from the refrigerant’s potential to exist in either a single-phase or two-phase state across substantial portions of the heat exchanger length. Such phase transitions engender variability in specific heats and convective heat transfer coefficients for the refrigerant.
Furthermore, analyzing each phase region independently is complicated by the intricate tube circuitry and the non-uniform heating or cooling of the airstream. Consequently, a precise analysis or design of a coil is most effectively accomplished by conducting energy balances on discrete, short segments of tubing.
If the tube segment length is judiciously chosen such that variations in fluid properties and convective heat transfer coefficients are minimized, an overall heat transfer coefficient can be employed for the energy calculations. This coefficient can be articulated in terms of thermal resistances, adhering to the methodology expounded in established heat transfer literature.
In the context of evaporator and condenser coils, the predominant factors influencing the aggregate thermal resistance are the refrigerant-side and air-side convection coefficients and the thermal contact resistance arising between the fin and the tube.
The refrigerant-side heat transfer coefficient is significantly influenced by the flow regime within the tubes, which can be either single-phase (liquid or vapor) or two-phase (a mixture of liquid and vapor). In the case of single-phase flow, established correlations for turbulent flow in tubes can be employed.
For two-phase flow, the heat transfer coefficient is a function of the refrigerant’s quality (mass fraction of vapor), the mass flux, and the tube’s geometry. The complex nature of two-phase flow necessitates the use of specialized correlations, often derived empirically, to accurately predict the heat transfer coefficient. These calculations are important in hvac systems.
In-tube augmentation techniques, such as the use of micro-fins or twisted tapes, can enhance the refrigerant-side heat transfer coefficient by increasing turbulence and promoting better mixing of the two-phase flow.
The thermal contact resistance between the fin and the tube is a critical factor affecting the overall thermal performance of the coil. This resistance arises due to the imperfect mechanical contact between the fin and the tube, which creates microscopic air gaps that impede heat transfer.
The magnitude of the contact resistance is strongly influenced by the manufacturing processes employed to assemble the coil. Factors such as the expansion method (mechanical or hydraulic), the expansion force, and the surface finish of the fin and tube can significantly impact the contact resistance.
Minimizing contact resistance is crucial for optimizing coil performance. Techniques such as using a tight fit between the fin and tube, applying a thermal grease or coating, and employing advanced bonding methods can help reduce this resistance.
The air-side heat transfer coefficient is primarily dependent on the airflow characteristics, including the air velocity, the fin geometry, and the spacing between the fins and tubes.
The fin geometry plays a crucial role in determining the air-side heat transfer coefficient. Factors such as fin density, fin thickness, and fin shape (e.g., plain, wavy, louvered) significantly influence the airflow pattern and the resulting heat transfer. It’s important to clean fins to maintain optimal efficiency. Coil cleaning is essential in hvac systems.
Optimizing the fin design involves balancing the need for a high heat transfer area with the requirement to minimize pressure drop across the coil. Advanced fin designs, such as louvered or offset strip fins, can enhance heat transfer while maintaining acceptable pressure drop levels.
The presence of lubricating oil in the refrigerant can significantly affect the heat transfer performance of the coil. Oil can increase the viscosity of the refrigerant, leading to a reduction in the heat transfer coefficient, particularly in two-phase flow.
Frost formation on the evaporator coil surface can severely degrade heat transfer performance by adding an additional thermal resistance and reducing airflow. Defrost cycles are often employed to mitigate the effects of frosting, but they can also reduce the overall efficiency of the system.
The arrangement of tubes within the coil, known as tube circuiting, plays a vital role in determining the overall performance of the coil. Proper circuiting ensures uniform refrigerant distribution and optimal utilization of the heat transfer surface. Factors to consider are the evaporator and condenser coils.
The Air-Conditioning, Heating, and Refrigeration Institute (AHRI) Standard 410, “Forced-Circulation Air-Cooling and Air-Heating Coils,” provides a standardized method for rating the performance of evaporator and condenser coils.
Eurovent Certification offers various certification programs for air conditioning products, including evaporator and condenser coils. These programs provide independent verification of product performance and energy efficiency.
Microchannel heat exchangers, characterized by their small hydraulic diameter channels, are gaining increasing attention as a promising alternative to traditional finned-tube heat exchangers. They offer advantages such as higher heat transfer coefficients, reduced refrigerant charge, and improved compactness.
The use of nanofluids, which are suspensions of nanoparticles in a base fluid, and enhanced surfaces, such as micro-structured or coated surfaces, are being explored as potential means to further enhance heat transfer in evaporator and condenser coils. HVAC engineers always try to improve heat transfer.
Additive manufacturing, also known as 3D printing, is emerging as a potential fabrication method for producing complex and customized coil geometries that can optimize heat transfer and reduce pressure drop.
Key Takeaways:
Air-cooled condenser coils are integral constituents of air conditioning and refrigeration apparatuses.
This article explores the intricate workings of your home’s HVAC system, focusing on the vital roles of evaporator and condenser coils.
This article provides a comprehensive overview of AC evaporator coil replacement cost, as well as condenser coil replacement cost, helping homeowners understand what to expect when facing this type of repair.
This document elucidates the principal factors influencing thermal exchange between the refrigerant and the airstream within a plate finned-tube heat exchanger
This article explains how your central air conditioner works, focusing on the critical roles of the evaporator and condenser coils.
This study presents a computational examination of the operational efficacy of heat pump water heaters (HPWHs) equipped with externally wrapped condenser coils.
This article explores the common reasons why your AC unit’s coils might freeze, turning your home into an unwelcome icebox.
This article dives into the common problems that plague AC condenser units, explaining why these issues occur and how they impact your air conditioning system’s performance.
This article delves into the common problem of refrigerant leaks in LG split AC units, specifically focusing on the debate between aluminum and copper condenser coils.
Your air conditioning unit is a complex system with many parts working together to keep your home cool and comfortable.
This article explores the crucial relationship between evaporator and condenser coils in your AC system, focusing on the importance of their size ratio for optimal performance in residential air conditioning.
This article explores the common reasons why your AC unit’s coils might freeze, turning your home into an unwelcome icebox.
This article dives into the common problems that plague AC condenser units, explaining why these issues occur and how they impact your air conditioning system’s performance.
© 2025 Condenser Coil All rights reserved.
Fill out the form below, our team can reply in 20 minutes.